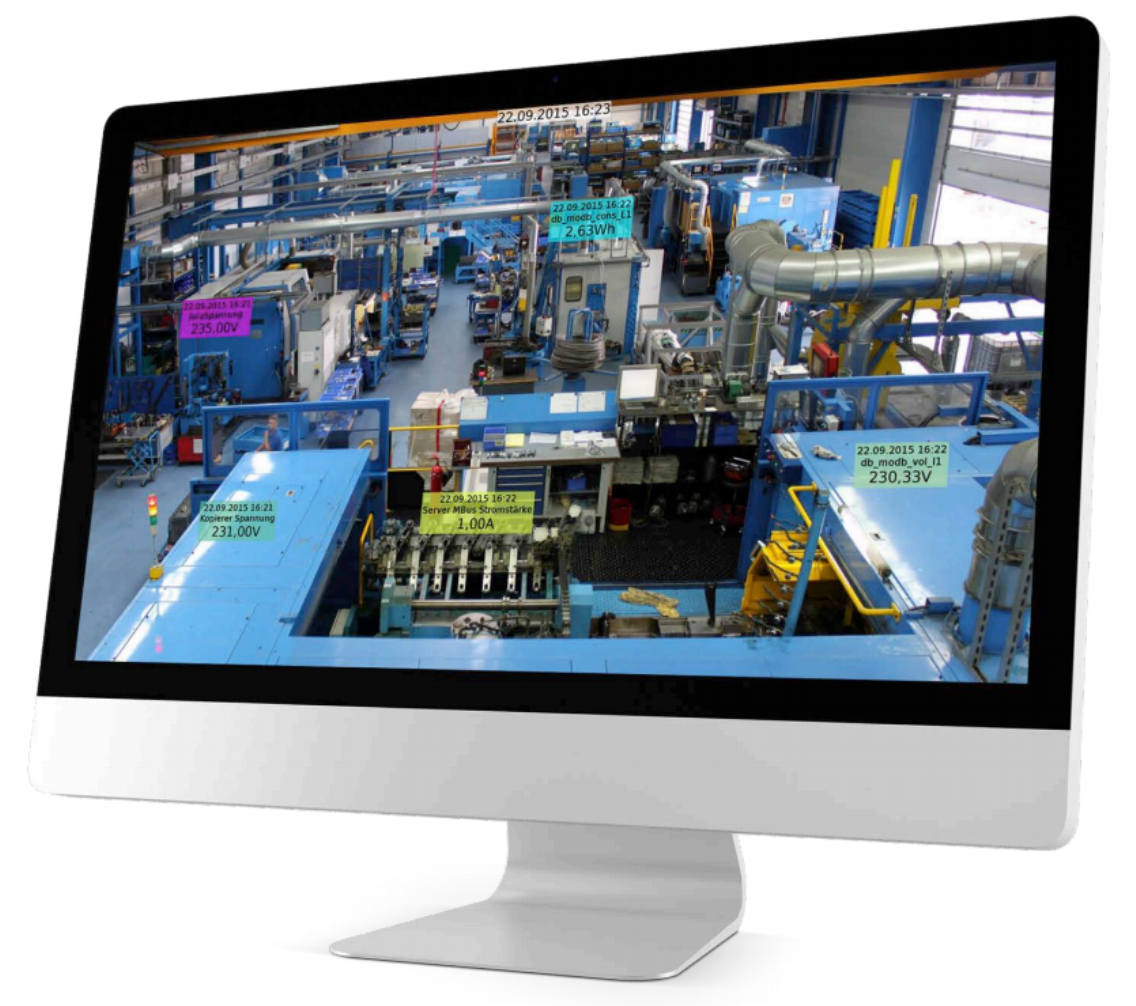
Higher machine availability
Reduce support costs by up to 50%
Technical equipment is subject to wear of machine parts in the production process, which depends on the local operating conditions. To conserve resources and reduce costs, "needs-based" and preventive as well as predictive maintenance makes sense. After all, economic goals can only be achieved if systems, machines and processes function properly.
With preventive maintenance, regular maintenance on machinery and equipment during operation ensures the functionality of the working equipment and reduces the probability of failure. This maintenance strategy reduces the number and severity of breakdowns and optimizes operating processes.
Predictive maintenance stands for maintenance based on the analysis of process and machine data. Real-time processing of the data enables forecasts and thus the basis for needs-based maintenance. This means that technicians are already busy rectifying an impending malfunction before a real problem arises.
The monitoring of plants and machines by the dibalog systems enables maintenance to detect wear as well as impending malfunctions in advance, i.e. with foresight, and allows maintenance to be carried out only when it is actually necessary.
Short facts
- digital temperature sensors available (for liquids, rooms, contact sensors for machines/pipes)
- additionally supports all common sensor and monitoring technologies
- recording of all activities like malfunctions, repairs and maintenance in central machine book
- as part of the dibalog EAS no additional basic hardware and communication technology required